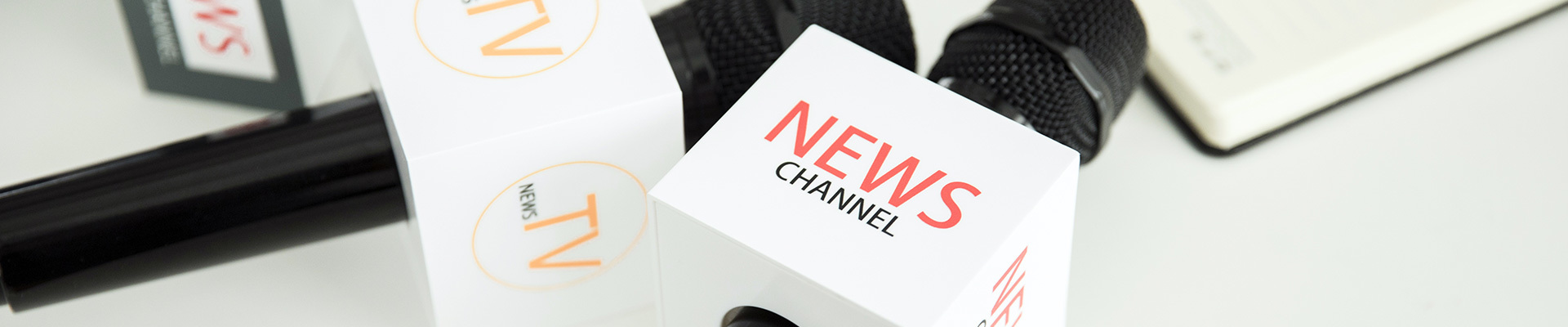
陽光書院 2022 第十八期
陽光兔業自我學習系列
陽光書院 2022 第十八期
<總第四十一期>
2022年8月4日
現場問題解決八步法,輕松實現現場管理
—1—
現場管理對生產型企業十分重要,這是每一位生產管理人員都有的共識。但作為生產現場管理人員,是否能夠判斷出生產現場存在哪些問題,并能及時找出問題的解決方案并組織改善,這是開展工作的必備能力之一。
—2—
不同工廠企業的生產現場都會存在不同方面、不同程度的問題,但是也存在著一定的共性,下面就是四種在現場管理中最常見的不足之處。
1、生產現場混亂
走進生產車間,如果原料、半成品、成品、報廢品和生產工具不加規整,隨意擺放,使車間顯得非常混亂,容易產生產品的品質問題,不良品較多;操作人員需要花費更多時間尋找所需的生產材料,會降低生產效率;管理人員無法統計出物品的數量,會造成管理的混亂和無序;過多地走動,增加了工作人員的搬運時間,會使車間的工作秩序出現問題。
此外,隨意擺放還易造成物品堆積,不僅浪費生產空間,通道不暢,也占用大量資金。
2、生產設備擺放不科學
生產現場的機器設備擺放不科學,也是工廠中常見的不良現象。生產設備的擺放直接關系到生產力的三個要素,即勞動者、勞動手段和勞動對象如何更好的結合的問題,合理的布置和擺放有利于企業提高生產經濟效益。
因此,在設備的安裝過程中,要優先考慮作業流程是否流暢,盡可能縮短機器設備間的距離,防止虛耗工時增加。
3、機器設備缺乏定期維護
有些生產企業的機器設備常年缺乏有效的保養和維護,機器設備上到處都是油污和灰塵, 影響了設備的使用壽命及機器精度,容易發生故障,增加了維修成本,影響了工作士氣,并直接影響了生產效率。此外,對設備的管理不善還會導致產品品質的下降,不利于企業長遠發展。
4、工作人員的整體形象不佳
工作人員儀容或者穿著不整齊,會給人非常懶散的感覺,損害工廠形象,也對工作士氣有比較大的影響,并且不同工種間不易識別,妨礙工序間的溝通協調。此外,工作人員的工作姿勢不當極易產生疲勞,進而降低生產效率,增加品質不良的幾率。
—3—
問題的發現比解決更重要,作為現場管理人員,熟悉現場但不能熟視無睹,要有一雙發現問題的眼睛,要對生產現場不滿意,經常發現問題并提出解決方案,然后組織改善活動。作為現場管理人員,需要的不只是解決一個問題,更重要的是掌握解決問題的方法。現場問題解決法(PDCA-SDCA)作為開展現場改善的基本方法,要解決的就不只是單個問題,而是如何去解決成百上千問題的思路。
下面給大家簡單介紹以十個基本意識為指導將通常進行改善的 PDCA-SDCA 過程,其中又細分成八個關鍵的步驟,整理出來形成指導改善開展的方法。
PDCA 指 Plan(計劃)→ Do(實施)→ Check(評價)→ Action(鞏固,改善) 計劃(Plan)是關鍵 充分而周到的計劃事半而功倍!
—4—
現場問題解決法(PDCA-SDCA)解決問題的具體行動步驟:
步驟 1:明確問題。思考工作的真正目的;思考工作的“理想狀態”;把握現狀;將差距 “可視化”。
步驟 2:分解問題。將大而模糊的問題分解,整理成自己能夠著手解決的具體問題。只有將問題充分分解,才能有效地找到真因。決定要解決的問題的優先順序,親赴現場 “現地現物”地去觀察生產問題的具體環節,搜集定量,定性的事實信息,將問題特定為具體的問題點。
步驟 3:設定目標。朝著解決問題的方向努力,設定較高的目標。在通往實現夢想的路上,懷著滿腔熱忱,帶著欣喜和勇氣去挑戰,一定能取得較大的成果。同時也能實現自身的成長。制定中長期的目標,并為達成最終的目標,制定一系列連續的短期目標
步驟 4:把握真因。調查為什么會發生問題,不斷地追問“為什么?”,抓住發生問題的真正愿因。追查原因不能想當然,也不把責任歸咎于他人,而應實事求是,反復追問“為什么?”
步驟 5:制定對策。在制定對策的時侯,不拘泥于固有觀念以及自己的工作范圍,不因困難而放棄,廣泛地從公司內外尋求建設性意見。從“效果”,“成本”,“時間”,“風險”的觀點來商討對策,制定實施計劃。要與相關人員和相關部門達成共識。
步驟 6:貫徹實施對策。齊心協力,迅速貫徹。通過及時地匯報、聯絡、商談共享進展信息。重視速度,遇到障礙進展不順時,不言放棄,堅持到底。
步驟 7:評價結果和過程。客觀地評價目標的達成結果和過程。從成功和失敗中學習, 積累知識和技能。
步驟 8:鞏固成果。將成功的過程制度化并固定下來。這樣即使從事這項工作的人發生變動,也能夠保證繼續創造成果。積極推廣成功的機制,以提高組織整體的戰斗力。
當員工真正養成了分析問題的思維及問題解決法,問題的解決就會更有成效。即使是基層員工,一旦擁有良好的思維習慣,誰能擔保他(她)不是下一個杰出人才呢?
“現場改善”的 13 個基本要點,工廠
生產管理高效 3 倍!
一、領導者要以身作則
不要認為“改善的工作是部下的事,上司不必去做這些”。事實上,不論是領導者還是員工,都必須要能致力于改善。如果他自己沒有辦法首先身體力行,那么其部下也就無法跟著前進。
作為領導者,每天都要督促自己力行改善,同時也要常常要求下屬人員“改善,再改善”,從而激發和提高下屬人員改善工作的意愿和情緒。
當然,領導者所進行的改善與生產現場一線作業人員所進行的改善的主題是不相同的。現場作業人員的改善是以作業程序和操作方法為主,而領導者則以組織、制度、管理體制等軟件方面的改善為主。
盡管兩者各自的具體改善對象和內容不相同,以身作則,并不斷督促部下要“改善,再改善”,但是上級人員如能為人表率、那么下屬人員就會增強改善意識,自覺貫徹上級的改善意圖。
總之,無論是領導者還是下屬人員,個人自身的不斷完善。都應該在工作的不斷改善之中,實現個人自身的不斷完善。
二、領導給部下分派任務,規定目標
有人誤認為領導者的工作就是給部下分派任務,規定目標;作為領導者,要求部下改善工作、制訂改善計劃、規定改善目標。而自己只等統計數字,這種做法是極不妥當的。
相反。不論下屬人員準備進行什么改善、做了哪些改善、改善中有哪些問題、改善的結果如何等,領導者都要對之給予關心,這是非常重要的。
例如,在質量管理小組成果發表報告會上,如果領導漠不關心,那么發言者自然會覺得不起勁,提不起精神,以后工作也沒有興趣。而如果領導能夠仔細聆聽部下的每一個改善報告,會對下屬人員改善的積極性產生影響,改善的熱情就會被激發出來。
三、不要輕視微不足道的改善活動
在生產現場,總會存在一些看來很不起眼的不合理現象或工作方法。然而,一些大事故往往出自于這些平時被人們忽視的環節上。所以,既要重視那些看來重大的改善活動,也不要輕視“小改善”。
“勿以善小而不為”,從點滴開始積累成完美。不要以為只有大改善才能稱得上是改善, 改善應該從小事做起,從身邊做起。
改善來源于“這樣做妥當嗎”,來源于小小的巧思,更來源于對日常工作的關心度,“處處留心皆學問”、“一屋不掃何以掃院子”、“勿以善小而不為”等是我們應該秉承的觀點。最開始的時候不要期望達到 100%,一次就成功的機會只有 1%,我們要不斷地改進。
四、要容忍失敗
領導者要容忍下屬人員改善活動的失敗,要認真聽取改善活動失敗的經過和教訓。實際上,事事成功是不可能的。而失敗本身就意味著需要改善。每一個失敗的事例都能為我們提供改善機會和防止再度發生的構想。
失敗并不重要,而重要的是不要使同樣的過失再度發生。一般來說,出現了失敗,當事者常常難于向上司啟齒。既然部下有勇氣將其失敗講出來,領導者就應對此給予贊許,并鼓勵他們繼續改善下去。因此,創造一種敢于說真話,敢于報告失敗的環境,對于“改善”來說是極為重要的。
五、越忙,越是改善的好機會
經驗表明,在那些工作比較清閑的車間里往往不會產生出更多的改善方案,并且也不會產生出水平較高的改善方案。
相反,在那些工作較忙的車間里,改善方案卻往往是層出不窮,而且還會出現高水平的改善方案。因為“忙不過來,人手不夠”,人們才會開動腦筋,想出解決辦法,激發出改善設想和改善方案。
當然,也會有“太忙了,顧不上改善了”的牢騷。這只能說明,這些人的改善意識和改善欲望不夠強烈。因此,他們也無法或者難以擺脫“忙不過來”的狀況。而不斷改善卻會使人們的工作變得輕松愉快,更加有效。
六、改善要根據實際需要
實際不需要的不必改善,實際工作中不急的放在次要時間,工作中需要的立即改善。
七、拋棄僵化固定的觀念
先否定現狀。改善中,改變觀念非常重要。不要認為這不能改那不能改,要相信“一切皆有可能”。
八、不強調理由
思考理由是退縮的開始,退縮的念頭一動,可以改善的事基本上就完了。比如立即行動進行改善的人不會以“客戶規定”為借口,只有不去行動的人才以“客戶規定”為借口。從不可能之中,尋找解決方法。
不要說“不可能”、“做不到”,所謂“不能做到”就是智慧不足。改善無處不在。不只在工作中存在改善的空間,日常生活中也一樣可以改善。例如電視主婦節目中用可樂瓶子斜切開做湯勺容器。兩個超市的大塑料購物袋可以疊成廚房圍巾等。
九、人人參與
不要個人英雄,人人皆可做改善,要靠集體的智慧和努力,何況改善不分大小,在一個制造部門內,應該有至少 50%的員工參與。
十、更應該重視不花大錢的改善
花錢的改善誰都會,我們需要花錢少甚至不花錢的改善,這樣一方面節省了開支,同時讓大家養成了嚴謹節約的好風氣。
十一、馬上行動
“重拙速,輕巧遲”,有改善計劃后不要過分拘泥于細節或者過度追求完美,要馬上付諸實施,哪怕只達到約定目標的 20%。
問題沒有馬上解決和不能馬上解決之分,出現問題要立即解決。精益生產所說的“執行要像暴走的人”就是這個意思。立即改正錯誤,是提高自身素質的必經之路。
十二、改善方法的四個原則
①現場原則。所有的工作都要在現場解決,我們的主管和工程師都要在現場。改善要遵從三現主義:現場、現物、現實。
②追查原因中的“五五法”原則,即通過五個為什么追問中發現問題原因。
③標準化原則。改善的第一步在標準化,沒有標準就沒有改善。
④重要度管理上的時間管理原則。
十三、改善無止境
改善的過程是個螺旋式上升的過程,永無止境。對待改善工作,就要像擰出一塊毛巾中的水一樣,而且擰干之后還要不斷地擰,改善工作也是如此。生產現場的情況并不是一成不變的,改善工作也不是一蹴而就和一勞永逸的事。
以往的改善在現在看來,也許又會發現一些不完善的部分,也許又可以發現更好的改善方法。人的能力在不斷地提高,新知識、新技術在不斷地涌現,人們不會也不應該滿足或停留在已有的改善成果上。
企業的環境在不斷地變化,顧客的需求也在不斷地豐富。因此,生產現場也不能只保持原有的狀況。總而言之改善是不會到頂的,而是無限的。
上述內容揭示了改善的基本觀念。事實上,質量和改善的根本問題是人的質量問題。只有全公司的所有工作人員都熱愛自己的公司,都熱愛自己的工作,公司的方針,都像一家人一樣來開展工作,都熱愛自己公司的產品,都遵循自己公司的事業才能長盛不衰,正因為如此,精益生產強調人的質量,注重對人性的尊重,重視對人的教育和培養。
上一頁
下一頁